Chiplet Technology 2025: Design Tools, Yield Challenges, and Market Adoption
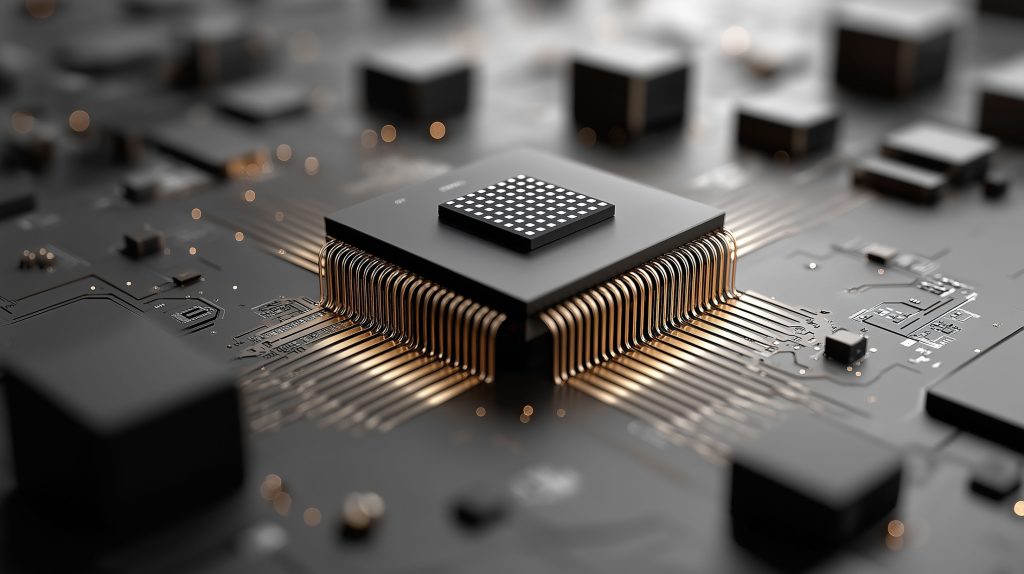
Overview of Chiplet Technology in 2025
Chiplet technology has emerged as a transformative approach to chip design, breaking large monolithic chips into multiple smaller chiplets that operate together in one package. This modular design offers key advantages over traditional system-on-chip (SoC) architectures. By partitioning complex systems into specialized dies (for compute, I/O, memory, analog, etc.), chiplets provide greater flexibility, allow mixing of different process nodes, and improve manufacturing yield and cost-efficiency creativestrategies.com semiengineering.com. As one analysis explains, “chiplets are small, and smaller dies improve wafer yields since the chance of a defect affecting a die diminishes with size. In a monolithic SoC, a single flaw can render the entire chip unusable” creativestrategies.com. Indeed, AMD reported that using a chiplet architecture in its EPYC server processors yielded up to 70% cost reduction compared to a comparable single-die design azonano.com – a testament to how higher yields and node optimization drive down cost per chip.
Beyond cost, chiplets help overcome scaling limitations. They sidestep the lithography reticle size limit (≈800 mm²), enabling construction of “virtual” larger chips by stitching multiple reticle-sized dies creativestrategies.com. High-performance processors like AMD’s Instinct MI300 use numerous chiplets to pack more transistors and functionality than a single die could creativestrategies.com. Chiplets also alleviate the “memory wall” by allowing memory dies (HBM stacks, SRAM caches) to sit close to logic dies on package, massively increasing bandwidth signalintegrityjournal.com. Advanced packaging techniques (e.g. 2.5D interposers like TSMC’s CoWoS) link these chiplets with high-density interconnects, achieving near-monolithic latency and bandwidth azonano.com.
In 2025, the semiconductor industry broadly recognizes chiplets as a key path forward as Moore’s Law slows azonano.com azonano.com. A recent IDTechEx report highlights that chiplets “provide enhanced flexibility and customization, leading to faster time to market and shorter upgrade cycles”, while also reducing costs and improving yields signalintegrityjournal.com. This has motivated leading players like AMD and Intel to adopt chiplet designs in flagship products (e.g. AMD EPYC CPUs, Intel’s Ponte Vecchio GPU) and underscores the growing importance of chiplets in high-performance computing signalintegrityjournal.com. Chiplets effectively decouple pieces of a system so each can use the most appropriate process technology – for example, high-density cores on 5 nm while I/O controllers remain on 16 nm – which maximizes performance-per-cost creativestrategies.com creativestrategies.com. “We anticipated that increasing core density in monolithic processor designs would become more difficult over time… One of the primary issues is that the process technology for CPU cores [is] on different innovation paths than the [analog] technology for memory and I/O. These two technologies are linked in monolithic processors and can impede swift product delivery,” AMD explained regarding its EPYC chiplet strategy creativestrategies.com. By disaggregating logic and I/O into separate dies, AMD “decoupled the innovation paths” for those components, allowing each to advance on its own timeline and optimal node creativestrategies.com. This modular approach – long theorized (even Gordon Moore suggested in 1965 that building “large systems out of smaller functions” could be more economical creativestrategies.com) – has finally become practical at scale, and by 2025 it is driving a paradigm shift in semiconductor design.
Crucially, chiplet-based design is not confined to one company’s vision; it is an industry-wide inflection point. Intel’s CEO Pat Gelsinger noted that advanced packaging and chiplets will enable chips with unprecedented transistor counts, stating that “EUV, advanced packaging with chiplets and other innovations will allow Intel to reach 1 trillion transistors per processor by the end of the decade” fierceelectronics.com. The market outlook reflects this optimism: analysts project the total value of devices using chiplets could reach $400+ billion by 2035, fueled by demand in data centers, AI, and other applications azonano.com azonano.com. In summary, as of 2025 chiplet technology is maturing from an experimental idea into a cornerstone of semiconductor roadmaps, promising to continue performance scaling through heterogeneous integration even as traditional scaling slows.
Design Tools and Integration Standards for Chiplets
Adopting chiplets requires new design methodologies and tools. Because a chiplet-based 3D-IC or 2.5D system is essentially a miniature system in a package, engineers must plan and verify at the system level rather than just the chip level ednasia.com semiengineering.com. In 2025, EDA vendors are rolling out solutions to handle the added complexity of multi-die integration. For example, at DAC 2025 Siemens EDA announced an “Innovator 3D IC” design suite to help architects “efficiently author, simulate, and manage heterogeneously integrated 2.5D and 3D IC designs” ednasia.com. This includes system-level floorplanning across dies and package, multi-physics simulators to model thermal-mechanical stress, and tools for 3D sign-off verification of inter-die connectivity and reliability ednasia.com ednasia.com. As Siemens’ Michael White described, these new tools aim to “dramatically reduce risk and enhance the design, yield, and reliability of complex, next-generation 2.5D/3D IC designs”, helping designers hit performance targets while maintaining yield and cost-efficiency ednasia.com. He characterized the shift to chiplet-centric design as an “inflection point” for EDA flows, requiring a system-centric approach from early planning through final sign-off ednasia.com.
Other major EDA providers have similarly expanded their offerings. Cadence and Synopsys now provide solutions for multi-die packaging co-design, interconnect modeling, and die-to-die interface IP. Notably, chiplet interfaces must be treated as first-class design objects. Traditional verification methods struggle with the web of interdependencies introduced by chiplets – signals cross chip boundaries via microbumps or interposers, creating challenges in latency, signal integrity, and power distribution semiengineering.com semiengineering.com. Modern chiplet-aware EDA tools address these by providing end-to-end system analysis of inter-chiplet links and enforcing compliance with interface standards semiengineering.com semiengineering.com. For instance, tools can analyze high-speed die-to-die SerDes links using IBIS-AMI models for both transmitter and receiver, automatically optimize equalization and terminations, and validate that the link budget meets standards like UCIe semiengineering.com. Automation features (e.g. connection wizards to map dozens of signals between chiplets) also significantly reduce manual effort semiengineering.com.
Standardized interconnect protocols are pivotal for chiplet integration. The industry in 2025 has largely rallied around UCIe (Universal Chiplet Interconnect Express) as a common die-to-die interface. UCIe 1.0 (launched in 2022) defines a universal PHY and protocol for connecting chiplets, supporting data rates from 8 to 32 GT/s with both short-reach and long-reach physical layers semiengineering.com semiengineering.com. It also provides robust signal integrity specs – eye masks, channel loss budgets, crosstalk limits – to ensure reliable high-speed communication between dies semiengineering.com semiengineering.com. The goal is to enable an open chiplet ecosystem where dies from different vendors or fabs can talk seamlessly on a package, much like USB or PCI Express did for plug-and-play components fierceelectronics.com. In fact, Intel, TSMC, AMD, Arm, Samsung and dozens of others formed a consortium to back UCIe, underscoring the broad industry support for standardization. By 2025, UCIe is seeing adoption in new designs (especially for accelerator-to-CPU connections and chiplet IP), though it’s still evolving and competing with some proprietary interfaces azonano.com. “Commercial viability [of chiplets] hinges on industry alignment around a set of chiplet standards, enabling car manufacturers to procure chiplets from the market and integrate them…,” noted Bart Placklé of imec, emphasizing why open standards like UCIe are critical beyond just technical elegance chiplet-marketplace.com.
In addition to electrical interconnect standards, designers leverage advanced packaging integration strategies. Approaches such as 2.5D interposers (silicon interposer with micro-bumps, e.g. TSMC CoWoS), fan-out wafer-level packaging (e.g. TSMC InFO), and 3D stacking with through-silicon vias are tools in the chiplet playbook 3dincites.com. Each integration style comes with design trade-offs in routing density, thermal dissipation, and cost. EDA tools now often include co-design capabilities that concurrently handle the chip floorplans and the package/interposer layout, since decisions in one domain affect the other ednasia.com. There’s also a push toward “digital twin” modeling of the multi-die system: for instance, Siemens’ flow uses a unified data model so that the package-aware context is present even when designing each die, and to ensure connectivity consistency when assembling chiplets onto the substrate ednasia.com ednasia.com.
A related aspect of chiplet methodology is modular design strategy and IP reuse. Once a chiplet (say a PCIe I/O tile or AI accelerator block) is validated, it can be reused across multiple products or generations with minimal redesign – akin to reusing silicon IP blocks, but at the die level creativestrategies.com azonano.com. Companies are increasingly designing chiplets with a “LEGO block” mindset, expecting to mix-and-match them. This has spurred the idea of a chiplet marketplace or catalog. By 2025, some third-party firms (e.g. Alphawave Semi) offer pre-built chiplets like high-speed SerDes, memory controllers, or AI engines that system integrators can potentially incorporate azonano.com azonano.com. Such trends remain nascent, but the vision of interchangeable chiplets is driving both EDA tool development and standardization efforts. In summary, the 2025 landscape for chiplet design tools is one of rapid evolution: smart EDA workflows, multi-physics simulators, and standardized interconnect IP are becoming essential parts of the toolkit that enables engineers to wrangle the complexity of multi-die systems semiengineering.com azonano.com.
Yield and Testing Challenges for Chiplets
While chiplets can improve per-die yields, they introduce new yield and testing challenges at the package and system level. In a monolithic chip, one needs to test and manufacture a single die; by contrast, a chiplet-based product is composed of numerous dies and their interconnections, multiplying the potential points of failure epdtonthenet.net. A primary concern is ensuring each individual chiplet is a Known Good Die (KGD) before assembly. “Unlike monolithic chips, chiplets require both individual die testing and system-level validation after integration. This demands specialized test infrastructure… Known-good-die (KGD) is the dominant approach, where each chiplet is fully tested before assembly to avoid yield losses at the package level,” as one industry publication explains 3dincites.com. Thoroughly testing bare dies is non-trivial: chiplets may have limited I/O access when not in a package, and traditional test pads consume precious area on these small dies epdtonthenet.net. Design-for-test (DFT) features and built-in self-test (BIST) circuits must be squeezed into chiplets to enable this pre-assembly screening, which can be challenging given area and I/O constraints epdtonthenet.net.
Even after verifying KGDs, integrating them poses additional hurdles:
- Die-to-die interconnect testing: Chiplets communicate through high-density interconnects (bump arrays, through-silicon vias, or hybrid bonding). Ensuring those links are defect-free and meet signal integrity requirements is crucial epdtonthenet.net. A tiny defect or misalignment in an array of thousands of micro-bumps can disable the channel between two chiplets epdtonthenet.net. Testing needs to cover not only digital correctness but also high-speed analog performance of these interfaces (eye openings, bit error rates, etc.), often requiring new test methodologies and equipment.
- System-level testing and burn-in: Once chiplets are assembled on the package, the complete system must be tested under realistic conditions. This includes validating that all dies work together at intended clock speeds, checking power delivery integrity across the package, and screening for thermal hotspots or other interactions epdtonthenet.net. 3D integrated packages complicate this – for instance, a stacked memory-on-logic chiplet might overheat underlying logic if not properly cooled, so system-level thermal test is needed epdtonthenet.net azonano.com. Gaining test access to internal signals deep in a multi-die stack is difficult; advanced techniques like embedded sensors or 1149.1/1687 embedded test networks are being explored.
- Lack of universal test standards: The industry has only begun to standardize how to test chiplet-based devices. Today, companies often develop custom test flows for their multi-die products epdtonthenet.net. This raises costs and complexity, especially when integrating chiplets from different vendors. Efforts are underway (for example, proposals to extend UCIe with test interfaces) to create universal chiplet test protocols, but in 2025 a true cross-industry standard is still “evolving” 3dincites.com epdtonthenet.net. Without common protocols, each new chiplet combination can face non-trivial bring-up and validation challenges.
All these factors tend to increase test time and cost. Each die may need to be tested at wafer sort, then again after packaging (and possibly intermediate tests after 3D stacking steps), lengthening the manufacturing flow epdtonthenet.net. The added complexity must be balanced against the yield gains chiplets provide. Indeed, yield management itself becomes more complex: achieving high final product yield means not just high yield per die, but also high assembly yield. Key yield challenges unique to chiplets include:
- Assembly-induced yield loss: When many dies are combined, the chance that one bad die or a bonding defect ruins the product increases. For example, placing 3 chiplets on a package with 99% placement success each would introduce ~3% package yield loss just from assembly, as noted in one analysis anandtech.com. Misalignment, voids in solder bumps, or thermal stress during packaging can damage otherwise good dies epdtonthenet.net. Each additional die or stacking interface is a new source of potential yield loss.
- Cumulative yield impact: If each chiplet has yield Y on its own, a system needing N chiplets might have a combined yield roughly Y^N if any die failing kills the whole. For large N, this can drop overall yield significantly epdtonthenet.net. The strategy to counter this is rigorous KGD testing and possibly redundancy. Some advanced designs include spare “tiles” or self-repair schemes so that a package can tolerate a defect in one of many chiplets, but this is complex and costly.
- Process node variability: Chiplet designs often incorporate advanced-node dies (e.g. 5 nm, 3 nm) which inherently have lower yields initially, as well as older-node dies. The variability across processes means each might have different defect profiles epdtonthenet.net. Ensuring consistent quality across all dies and assembly steps is an “exponentially more difficult” problem than yield optimization on a single process epdtonthenet.net.
- Thermal and mechanical reliability: Heterogeneous materials in a package respond differently to heat and stress. During operation or thermal cycling, differences in expansion coefficients can induce stress, potentially causing micro-cracks, delamination of interfaces, or bump fatigue over time epdtonthenet.net. Hotspots in one chiplet can affect neighboring dies’ reliability if not mitigated epdtonthenet.net. These reliability issues effectively tie into yield, since failures in the field are yield losses from a product reliability standpoint.
Addressing these challenges is an active area of innovation. Testing techniques like built-in self-test (BIST) and hierarchical DFT are being refined so each chiplet can self-verify critical functions and then interoperate tests with neighbors azonano.com. Some companies are developing modular test sockets or board solutions to test multiple chiplets together before final assembly, approximating the end system environment. Additionally, analytics and AI are being used to predict which dies are likely to fail in packaging (using defect density data, wafer maps, etc.) so that bad combinations can be avoided epdtonthenet.net. The industry recognizes that without advances in test, yield, and reliability strategies, the economic benefits of chiplets won’t be fully realized – so in 2025 there is strong focus on known-good-die assurance, standardized test interfaces, and new reliability models tailored to multi-chip products epdtonthenet.net 3dincites.com.
Market Adoption Trends in 2025
By 2025, chiplet-based designs have been embraced by virtually all leading semiconductor players, especially in high-performance domains. This section examines adoption by key companies and across major market verticals:
High-Performance Computing and AI
The data center and AI accelerator segment is at the forefront of chiplet adoption. AMD was an early pioneer – its EPYC series server CPUs (since 2019) use a chiplet architecture with multiple CPU core dies (“Core Complex Dies”) plus an I/O die in each package creativestrategies.com creativestrategies.com. This approach has paid dividends: AMD can mix-and-match different core-count chiplets to create a range of SKUs, reuse chiplets across generations, and leverage the yield benefits of smaller dies. For instance, the 4th Gen EPYC (planned with up to 192 cores) continues this modular trend and even introduces 3 nm core chiplets paired with 6 nm I/O dies creativestrategies.com. AMD’s success with chiplets (helping it deliver more cores and better perf/$ than competing monolithic server CPUs) has prompted others to follow suit. Intel – which long built giant monolithic Xeon chips – shifted strategy and is now fully invested in multi-die architectures for servers and AI. Intel’s flagship data-center GPU, Ponte Vecchio, is a showcase of chiplets: it integrates 47 different chiplets (compute tiles, cache tiles, memory, I/O tiles) using EMIB and Foveros 3D stacking, achieving exascale-class performance that would be impossible on a single die azonano.com. Ponte Vecchio, deployed in the Aurora supercomputer, underscores how chiplets enable integrating heterogenous functions (GPU cores on 7 nm, RAM cache on 10 nm, I/O on 14 nm, etc.) in one powerhouse module signalintegrityjournal.com.
Nvidia has likewise charted a path toward chiplets to keep up with exploding AI compute needs. While Nvidia’s current flagship GPU (H100 “Hopper”) is still monolithic, the company introduced the Grace Hopper “Superchip”, which is a multi-chip module combining a 72-core Grace CPU die and a Hopper GPU die on the same package for AI and HPC workloads azonano.com. By 2025, Nvidia is expected to unveil its next-gen GPU (codename Blackwell) using a multi-die approach: industry reports indicate it will use two large GPU chiplets tied together by a 10 TB/s die-to-die interface, effectively creating a single GPU out of two reticle-sized dies creativestrategies.com. This “dual-chiplet GPU” strategy allows Nvidia to bypass reticle limits and improve yield (each die can be smaller) while delivering an aggregate 200+ billion transistor GPU for AI training creativestrategies.com. In fact, the modular multi-die design is becoming essential for leadership AI chips – even specialized AI startups are adopting it. For example, Cerebras famously went to the other extreme with wafer-scale chips, but others like Graphcore and Tenstorrent are exploring chiplet-based accelerators that package AI cores alongside memory and networking chiplets. The high-performance market clearly sees chiplets as a competitive advantage: as one analyst noted about Intel’s approach, if they can perfect chiplet integration, “it could give Intel a major cost and time-to-market advantage” by reusing “smaller and older tech chiplets” and leveraging cheaper older fabs for non-critical functions fierceelectronics.com. In summary, in the HPC/AI arena, chiplets are now mainstream, powering CPUs, GPUs, FPGAs, and AI engines by AMD, Intel, Nvidia, and others. The server sector drives significant adoption, as high-end customers (cloud providers, supercomputing centers) demand ever-higher performance that only multi-die scaling can provide signalintegrityjournal.com.
Mainstream PC and Mobile Computing
In 2025, chiplets are also influencing mainstream computing markets like PCs – though adoption here is more gradual, balancing cost vs. benefit. Desktop and laptop processors are beginning to incorporate chiplet (or “tile”) designs. Intel’s 2023 release of Meteor Lake for laptops is a prime example: it’s a client CPU built from four chiplets (compute tile, GPU tile, SoC I/O tile, and an base tile using Foveros 3D stacking) instead of one die fierceelectronics.com. This marks a break from Intel’s monolithic legacy and mirrors what AMD did in desktops. Intel plans to continue this roadmap, with Arrow Lake and Lunar Lake (2024–25) also using multi-tile 3D architectures across the client portfolio fierceelectronics.com. By using chiplets (which Intel calls “tiles”), Intel can mix process nodes (e.g. high-performance cores on Intel 20A, low-power cores or graphics on Intel 3) and even potentially integrate third-party IP. Intel is also supporting UCIe and an “open chiplet ecosystem” for its foundry customers, envisioning that future PC SoCs might integrate chiplets from various sources via standardized interfaces fierceelectronics.com.
AMD’s consumer CPUs likewise continue to use chiplets at the high end – e.g., Ryzen 9 desktop processors have two 5 nm core chiplets plus a 6 nm I/O die. However, for cost-sensitive segments (budget PCs, mobile SoCs), chiplets are still weighed against simpler single-die implementations. AMD CEO Dr. Lisa Su noted that at some price points (around sub-$200 CPUs), the added packaging cost of chiplets might outweigh their benefits, whereas for $300+ processors chiplets clearly make financial sense anandtech.com anandtech.com. Still, as silicon area requirements grow, the “tipping point” is moving downward; even mid-range devices may soon cross the threshold where chiplet designs become optimal anandtech.com anandtech.com. Meanwhile, mobile phone SoCs as of 2025 largely remain single-die (to minimize cost and because phone power budgets are lower). But the industry is eyeing chiplets for advanced mobile needs too. The IDTechEx analysis predicts mobile processors will adopt chiplets to achieve higher functionality and efficiency signalintegrityjournal.com. A foretaste of this is Apple’s M1 Ultra (used in high-end desktops): Apple essentially took two M1 Max chips and connected them via an ultra-fast silicon interposer, creating a bigger chip module. Although not marketed as “chiplets,” this demonstrates Apple’s ability to scale modularly. It’s conceivable that in a few years, smartphone platforms might integrate, for example, a baseband/RF chiplet and an AP (applications processor) chiplet in one package for tighter coupling, or stack specialized neural engine chiplets to boost AI performance on-device.
Additionally, memory and storage subsystems in consumer devices are leveraging chiplet-like integration. High-bandwidth memory (HBM) stacks are already a form of chiplet (DRAM dies on logic base die). There is also exploration of chiplet-based chip-and-memory combos for phones (to save PCB space by co-packaging DRAM with the CPU). While not yet ubiquitous in 2025, these trends point to a broadening adoption beyond just the highest-end systems.
Automotive and Other Verticals
The automotive industry has historically been conservative in adopting the latest semiconductor packaging due to extreme reliability requirements (cars may need 15-year lifespans under harsh conditions). However, the surge in computation for advanced driver assistance systems (ADAS) and autonomous driving is forcing a reevaluation. By 2025, the automotive sector is actively exploring chiplets as a way to meet performance needs while managing costs and product flexibility chiplet-marketplace.com chiplet-marketplace.com. Imec (a leading research institute) launched an Automotive Chiplet Program in late 2024, bringing together carmakers (BMW), Tier-1 suppliers (Bosch, Valeo), chip IP companies (Arm, Synopsys, Cadence), and startups (SiliconAuto, Tenstorrent) to define how chiplets could be used in vehicles chiplet-marketplace.com chiplet-marketplace.com. The consensus is that chiplets could enable a “disruptive shift in central vehicle computer design”, offering “rapid customization and upgrades, while reducing development time and costs,” according to imec’s VP of automotive, Bart Placklé chiplet-marketplace.com. The ability to mix-and-match dies would let automakers tailor SoCs for different models by combining standard compute chiplets with custom ones for, say, sensor fusion or safety isolation. However, Placklé also cautions that “moving to a chiplet architecture is prohibitively expensive for OEMs if done in isolation” – meaning it only makes sense if the whole auto industry coalesces around common standards and can source chiplets from a robust supplier ecosystem chiplet-marketplace.com. In other words, automotive needs an open marketplace of chiplets (and long-term support assurances) to make this viable.
Technical moves are underway to meet automotive needs. TSMC, for example, announced plans to offer automotive-qualified chiplet packaging by 2025, adapting its 3DFabric integration technologies (InFO and CoWoS) to meet automotive reliability and quality standards chiplet-marketplace.com. The first design kits for an automotive-grade InFO-based chiplet process are expected by late 2025, enabling multi-die integration on a package that can handle automotive temperature and stress profiles chiplet-marketplace.com. Automotive-focused chips (such as those from NXP, Renesas, Mobileye, etc.) are still mostly monolithic in 2025, but next-generation designs for autonomous driving compute are likely to incorporate chiplets. In fact, Renesas has teased a future 3 nm “chiplet extension” of its automotive SoCs chiplet-marketplace.com, and Tesla’s self-driving chip team is rumored to be evaluating multi-die approaches for their next AI processors. The hesitation is fading as the need for HPC in cars grows: as Siemens EDA’s Michael White noted, even automotive applications (like autonomous driving) are “driving the need for 3D ICs”, not just hyperscale datacenters ednasia.com.
Beyond data center, consumer, and automotive, chiplets are making inroads in other verticals:
- Telecommunications and 5G/6G infrastructure: Network equipment can benefit from chiplets by integrating high-speed analog/RF chiplets with digital baseband processors. This heterogeneous integration improves performance and allows upgrading one part without redesigning the entire SoC. The IDTechEx report identifies telecom and IoT as key sectors where chiplets enable more efficient solutions signalintegrityjournal.com. For example, a 5G base station IC could use an RF front-end chiplet at an optimal node for analog, alongside a DSP chiplet on an advanced node for signal processing – all in one package to minimize latency azonano.com.
- Aerospace and Defense: These industries often need high-performance, radiation-hardened electronics in low volume, which historically leads to using older nodes or FPGAs. Chiplets offer a way to incorporate cutting-edge processing (from commercial nodes) with specialized chiplets (for rad-hard IO or encryption) in one package. The U.S. DARPA has run programs (CHIPS, AFRL projects) demonstrating multi-vendor chiplet interoperability for defense systems fierceelectronics.com. In one case, Intel showed an FPGA with analog and digital chiplets from different foundries integrated together to meet a defense use-case, at a fraction of the development time of a custom SoC fierceelectronics.com.
- Edge and IoT devices: Modular chiplets can help tailor edge processors to specific needs (e.g. adding an AI acceleration tile to an otherwise standard microcontroller). While still early, some industrial and edge AI modules are adopting this approach to scale performance without a full custom redesign azonano.com.
In terms of key players driving the market in 2025, AMD and Intel stand out for widely deploying chiplets in high-volume products (CPUs, GPUs) signalintegrityjournal.com. TSMC and other foundries/OSATs are crucial enablers, providing the advanced packaging services that make chiplet integration possible – TSMC’s CoWoS and SoIC packaging are used by many (AMD, Apple, etc.), and Intel is offering its own advanced packaging (EMIB, Foveros) through its foundry program to partners. Nvidia, while slightly later to multi-die GPUs, has embraced the concept with its Grace CPU + Hopper GPU combos and forthcoming tiled GPUs. Chiplet IP companies and startups (like Marvell, AMD Xilinx division, Alphawave, Eliyan, etc.) are also part of the ecosystem, creating standardized chiplet interconnect IP and demonstrating test chips (for instance, startup Eliyan demonstrated a 5 nm chiplet interconnect PHY running at 64 Gbps, showcasing high-speed die-to-die communication without an expensive interposer chiplet-marketplace.com).
To quantify the trend: analysts note that “leading companies like AMD and Intel have adopted chiplet designs” in major products, and this “widespread adoption underscores the growing importance of chiplets in high-performance computing” signalintegrityjournal.com. By 2025, chiplets are no longer a niche experiment but a mainstream design philosophy for CPUs, GPUs, and beyond. According to IDTechEx, we are seeing chiplet technology play a “crucial role” not just in servers but across PCs, mobile, telecom, and automotive, with each sector finding unique benefits in the modular approach signalintegrityjournal.com. The market is thus poised on a steep growth curve as these concepts move from pilot to production.
In conclusion, chiplet technology in 2025 stands at an exciting juncture: powerful design tools and standards are coalescing to support multi-die architectures; yield and test challenges, while significant, are being addressed through innovation in KGD testing and packaging reliability; and market adoption is accelerating, led by industry giants and expanding into new verticals. As we head toward 2030, the consensus is that chiplets will be a foundation for the next era of semiconductor innovation – enabling the industry to continue scaling performance, power, and cost in ways that a purely monolithic approach no longer can azonano.com signalintegrityjournal.com. Or, in the words of one expert, “the chiplet revolution is here… offering unprecedented flexibility and cost advantages,” and with the right standards and tools in place, engineers can “navigate the complexity and deliver innovative, high-performance systems” that meet the demands of emerging applications in AI, automotive, and beyond semiengineering.com semiengineering.com.
Sources:
- M. White (Siemens EDA), “Latest EDA Tools Target Chiplet Integration, Package Verification,” EDN Asia, Jul. 2025 ednasia.com ednasia.com.
- M. Clancy, “Mastering Chiplet Design,” Semiconductor Engineering, Jun. 2025 semiengineering.com semiengineering.com.
- C. A. Patil, “Test & Yield Challenges of Chiplet-Based Products,” EPDT, Dec. 2024 epdtonthenet.net epdtonthenet.net.
- A. Singh, “What Is a Semiconductor Chiplet…Chip Design?” AZoNano, Jul. 2025 azonano.com azonano.com.
- Signal Integrity Journal (IDTechEx report summary), Oct. 2024 signalintegrityjournal.com signalintegrityjournal.com.
- N. Flaherty, “TSMC plans automotive chiplet process for 2025,” eeNews Europe, May 2024 chiplet-marketplace.com.
- Imec Press Release, “Imec’s Automotive Chiplet Program,” Oct. 2024 chiplet-marketplace.com.
- M. Hamblen, “Intel CEO Gelsinger… focuses on chiplets,” Fierce Electronics, Aug. 2022 fierceelectronics.com fierceelectronics.com.
- B. Reischl, “Chiplets and the Future of System Design,” Creative Strategies, Aug. 2023 creativestrategies.com creativestrategies.com.
- 3D InCites (Micross), “Chiplets: Optimized Integration…,” Jun. 2025 3dincites.com.